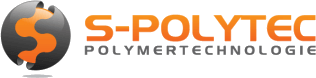
CO2 laser cutting in plastics processing offers numerous possibilities that would not be possible with milling or cutting by sawing.
CO2 laser cutting is a process with which parts made of plastic can be lasered with high precision. The non-contact process ensures that even delicate work is possible. At the same time, some of the work steps involved in conventional sawing or milling are eliminated. The lasered material is vaporised so that no chips are produced. Problems such as breakage and offcuts can also be minimised with this process.
CO2 laser cutting is a process that works with a special gas laser. The medium of the laser is therefore a gas or a gas mixture. In most cases, a CO2-N2-He gas mixture is used. By supplying energy through a voltage discharge, light waves are generated. The laser tube is equipped with a mirror at both ends. One of the mirrors is partially transparent, while the other is opaque. The resulting light waves are reflected from one mirror to the other until they emerge from the partially transparent mirror.
This technical arrangement is called an optical resonator or laser resonator. The resonator generates the CO2 gas laser using high electrical voltages of more than 15,000 volts. A CO2 atom that is at a high energy level is forced by a light particle or photon to a lower energy level. In the process, it also emits a photon. As a result, the existing photon is retained on the one hand, while the new photon is added. Both photons in turn stimulate new transitions to lower energy levels. The result is a kind of chain reaction in which the laser builds up. Depending on its field of application, the CO2 laser can create engravings or ablate and cut material. CO2 lasers can not only be used to laser parts made of plastic, but also to generate barcodes or product and serial numbers.
CO2 laser cutting is used in manufacturing where precise work and high flexibility are required. Conventional cutting techniques often do not achieve the desired quality standard that is possible with laser cutting. In the cutting process, the processed material is first heated beyond its melting point. Plastic waste produced in the process is blown out of the kerf with a gas. When it comes to laser cutting thin plastics, the laser beam is redirected to the kerf via a deflection mirror. The plastic melts within a few fractions of a second, causing it to be cut precisely. The thinner the plastic to be processed, the higher the possible cutting speed. The resulting cone at the edges of the plastic workpiece is all the finer the thinner the plastic.
Certain materials are particularly suitable for laser processing. Basically, all thermoplastics are considered ideal materials for processing by CO2 lasers. Thermoplastic materials show a change in microstructure as a result of the heat effect. In this way, particularly clear cut edges are possible in the plastics during laser cutting. Mechanical finishing is no longer necessary.
Typically, acrylic glass (also known under the brand name Plexiglas®), polypropylene, as well as polyamide (PA) are among the plastics that can be processed with the CO2 laser. ABS, ASA/ABS, SAN or PUR can also be processed without any problems using the laser cutting process.
Some plastics are unsuitable for laser processing for health reasons. These include, for example, PVC (polyvinyl chloride) and PTFE (also known under the brand name Teflon®). Polycarbonate (PC) is also considered unsuitable. Similarly, sheets or profiles made of polyethylene terephthalate glycol (PET-G) are less suitable. Multilayer high-pressure laminate (HPL) or sheets with an aluminium top layer should also not be processed by laser. The laser processing of thicker plastic sheets (from about 10 millimetres thick) is still considered problematic.
Companies that have parts made of plastic lasered include acrylic processing firms. They often produce displays, for example, which benefit from the precise cutting processes. CO2 laser cutting is also used to produce signs or lettering from this material.
Furthermore, the cutting of plastic foils is one of the most important markets for the use of CO2 laser systems. This area of application concerns the automotive industry in particular. But also front panels for various household appliances are made of plastics, the cuts of which are often created with laser systems. Keyboard foils are also often made of corresponding plastics. Another important core market is the textile industry. Laser cutting systems are increasingly used in technical textiles such as filter media. Artificial plush materials in the toy industry are also among the markets.
The primary advantage in the use of CO2 laser cutting technology is the precision cut. Anyone who has parts made of plastic laser-cut benefits from the finest contours. Cut edges run precisely, so that polished cut edges are also possible. The cut is accurate and burr-free. CO2 laser cutting is characterised by a narrow cutting gap and a low heat-affected area. Depending on the thickness and type of material, a cutting accuracy of between 0.05 and 0.1 millimetres is possible.
CO2 laser cutting ensures the best possible utilisation of the available material. Cutting takes place without contact, so that no chips or other waste are produced. On the one hand, this has the advantage that there are no chips to dispose of. On the other hand, there is no need for mechanical reworking. The plastic blank is thus ready for further use immediately after laser processing. This ensures maximum productivity and high flexibility at the same time.
This is associated with the advantage of fast processing with cost savings. The laser cutting systems are easy to operate. This eliminates lengthy set-up times. The set-up costs also remain within limits, as some additional applications and tools can be saved. The laser itself works in a time-saving manner due to its high power. Depending on the amount of work and the area of application, CO2 lasers exist in different power classes. This makes it possible to realise both small and large runs of plastic blanks.
Laser cutting of plastic using CO2 lasers is gentle on the material. Thanks to the non-contact technology and the small heat-affected zone, there is little to no mechanical stress. The processed materials are not damaged. This even applies to painted or printed surfaces. Thanks to the process, the print or lacquer coating remains undamaged.