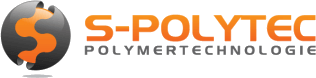
For holes for mounting our plastic panels, we offer you drills in various designs. From VHM drills for HPL panels to ground HSS drills in various sizes to match our stainless steel screws, rivets or spacers.
Incl. 19% Tax
Incl. 19% Tax
Incl. 19% Tax
Incl. 19% Tax
Incl. 19% Tax
Incl. 19% Tax
Incl. 19% Tax
Incl. 19% Tax
Incl. 19% Tax
Incl. 19% Tax
Incl. 19% Tax
Incl. 19% Tax
Plastics can be machined very easily and drilling plastic sheets is one of the most common processing methods. Starting with drill holes for screwing plastic parts together, to drill holes for wall signs that are to be mounted on the wall with spacers, to flat cladding of facades and balcony surrounds that are to be fixed by screwing or riveting. Different drills are required depending on the area of application and plastic. For this reason we offer in our online shop various drills made of different alloys and in different diameters.
For plastics with very hard surfaces, such as our HPL sheets, our solid carbide drills are most suitable, as they are very hard and have a special drill head geometry that prevents the decorative surfaces from tearing out during drilling. However, here too, a distinction must be made between sliding points and fixed points during installation, so that different drill diameters are required. Whether the HPL panels are fastened with façade screws, balcony screws or façade rivets is not of great importance. However, the drilling of the fixing points in the substructure may again require different drills and in this case it is definitely of significance whether the installation is done by riveting or screwing.
The HSS drills that we offer in our online shop are suitable for all plastics that we offer in our online shop with the exception of HPL boards. Thus, our acrylic glass plates can be provided with holes to mount them on the wall as signs with our stainless steel spacers. Our aluminium composite panels can also be excellently drilled with HSS drills to use them as signs or wall cladding. The same applies to substructures made of aluminium or steel. However, please note the diameter, which can vary depending on the mounting material.
TIP: We have listed separately in each individual product which drills are required for which mounting material.
HPL boards are very compact, rigid boards consisting of several layers of paper soaked in resin and pressed under very high pressure to form a solid board. This is why the panels owe their abbreviation HPL, which is derived from the English language for High Pressure Laminate. The hardness of the boards poses a particular challenge when drilling, as drills made of correspondingly hard alloys are also required for this. Drilling with a conventional HSS drill is certainly possible, but the life expectancy of the softer drill is considerably shorter than with a drill made of hard metal.
In order to ensure that drilling HPL panels is still possible without any problems, our online shop offers solid carbide drills. Due to their very high hardness, these are not only excellently suited for drilling the very hard decorative panels, but also have a special drill head geometry that prevents the decorative surfaces from breaking off or splintering at the edges of the drill hole. To prevent the drill from slipping, our solid carbide drills are also equipped with a very sharp centre point. Depending on the intended use, different hole sizes and corresponding drills are required when drilling HPL panels. For facades and balconies, a hole with 6mm is usually defined as the fixed point and all other holes of a panel are drilled with 8mm. The larger sliding point drill holes are intended to prevent the panel from bowling in the event of thermal expansion of the panel and provide sufficient clearance for expansion.
If HPL panels are used for cladding facades or as balcony surrounds, it is very important that they are installed without constraint. Therefore, please also pay attention to the instructions of the installation material used with regard to tightening torques of screws or the use of special gauge mouthpieces for riveted connections.
TIP: Before drilling HPL panels, always pay attention to the installation instructions for the intended use.
Aluminium composite panels are manufactured in sandwich construction and consist of a plastic core of polyethylene and cover layers of thin aluminium. For this reason, a drill bit for metal is also the best choice for drilling aluminium composite panels. With our ground HSS-G drills, we offer you the right drills for the most common applications of the popular sandwich panels. The sharp drill glides easily through the aluminium surface layers and also transports the drill chips of the PE core cleanly to the outside.
If aluminium composite panels are used to cover balcony surrounds or facades, one hole on the panel should be selected as a fixed point. The remaining holes are drilled larger as sliding points. While the sliding points can be made with an 8.0 mm HSS drill or a 10.0 mm HSS drill, the way in which the aluminium composite panels are to be fixed is important for the fixed points. For façade screws on a wooden substructure, as well as for our balcony screws with M5 thread, the sliding point should be drilled with a 6mm diameter drill. If, however, the cladding panels are fastened to an aluminium substructure with our facade rivets, the fixed points should be drilled with the drill that matches the rivet. With our facade rivets this corresponds to a drill bit diameter of 5.1mm. The substructure itself should be drilled with the same drill bit size as used for the fixed points. Exceptions are substructures made of wood, because the wood does not necessarily have to be pre-drilled for the facade screws.
Aluminium composite panels are often used in advertising technology for inscribed company signs or billboards. Especially in combination with our high-quality spacers made of stainless steel, this creates a visually appealing advertising space. Wall spacers are available in many designs and diameters, which require different sizes of holes in the panels depending on the size. Please refer to the respective product description of our spacers for information on drill diameters.
TIP: If aluminium composite panels are used as cladding panels, it is imperative to ensure that they are installed without constraint.
Drilling plastic panels is not particularly difficult and can be done with simple drills made of conventional tool steel. However, ground HSS drills, as we offer them in our online shop, are the better choice, because they are not only characterised by their self-centering drill tip, but also have ground cutting edges, which contribute to a much better visual appearance of the hole in relation to the edges of the drill hole. The twist of the spiral removes the chip very well. Especially with soft plastics such as polyethylene or polystyrene, where considerably lower speeds are required, this significantly reduces the fusion of the chip with the drill or the edges of the drill hole.
Drilling brittle, hard plastics such as acrylic glass or even polypropylene can also be carried out very well with an HSS-G drill bit, but here again, attention should be paid to a low speed and also the pressure on the drill bit should be very low in order to prevent the edges of the drill hole from breaking or the plate from breaking. In this case, a solid carbide drill can make a significant contribution to ensuring that the edges of the drill hole are extremely precise. The elongated twist of the spiral removes the chip even better than with an HSS drill. In addition, the angle of twist causes more effective cooling of the drill and the drill hole itself, which further reduces the risk of the chip fusing due to excessive heat development. It should be noted, however, that brittle plastics with a high surface hardness should be placed firmly on a flat surface to prevent flutter or vibration of the plastic sheet. Otherwise, this can result in the plate breaking.
It is not only the choice of drill that is decisive for the later use, but also the diameter of the hole. Depending on whether the drill holes are to be used for subsequent screwing or mounting, placed as a perforated plate for covers with a cooling air circulation or placed purely for optical reasons, the choice of the correct drill size can be decisive. For riveting, the drill should always be one to two tenths of a millimetre larger than the rivet sleeve. Depending on the thermal expansion of the plastic and the type of assembly, it is also important to consider whether a constraint-free assembly with fixed and sliding points is required. When mounting with spacers, the drill must be chosen large enough so that the cover can be screwed or inserted through the hole in the sleeve, but small enough that the hole is still completely covered by the cover.
VHM solid carbide drills are basically no different from HSS drills in terms of their design. However, as we have developed the drills especially for drilling our HPL plates, our solid carbide drills have a different geometry for the drill head, which is also equipped with a very fine and extremely sharp centre point in order to be able to drill through the hard surfaces precisely and cleanly without having to fear the drill slipping or splintering at the edges of the drill hole. As usual for drills made of solid carbide, our special drills with long twisted spiral are characterised by a very good chip evacuation, which is also an advantage with softer or brittle plastics and produces very short chips.
Drill bits made of solid carbide are characterised by enormous tool life, which cannot be achieved with conventional HSS drills. The higher rigidity allows a higher feed rate without this having a negative effect on the very long service life. Due to higher cutting speeds, significantly shorter working times are possible, which results in a price advantage, especially when drilling many holes.
HSS drills also belong to the cutting tools, but are mainly used for metalworking. The abbreviation HSS is derived from the English term High Speed Steel. This is a high-alloy tool steel, which is also known in German as Schnellarbeitsstahl or high performance cutting steel. Compared to a drill made of solid carbide, this alloy is softer and therefore less susceptible to vibrations or impacts, but is only conditionally suitable for higher cutting speeds on very hard materials.
It should be noted that when drilling metals, the speed must be reduced as the drill hole diameter increases. While larger speeds can be selected for very small drill diameters, it is very important to drill more slowly for thicker drills to prevent the drill from burning up. The pressure on the tip of the drill should also be kept extremely low to prevent premature wear. Coolants (e.g. drilling paste, cutting oil or cooling lubricant) can significantly extend the life of an HSS drill. When drilling plastics, the speed should always be reduced significantly anyway. This prevents the drill from heating up too much and the drill chip from fusing with the drill hole.
HSS drills are available in many different designs and grindings, regardless of the drill diameter. The most common types are HSS-R drill, HSS-G drill and HSS-E drill. HSS-R drills made of rolled steel are the cheapest type. Their simpler quality is characterised by good chip removal and high breaking strength. HSS-G drills are ground drills which are milled and hardened from one piece and are self-centering due to the drill head geometry. This enables higher accuracy and more precise drilling than with a simple HSS-R drill. In addition, HSS-G drills have a better service life than the cheaper rolled HSS drills. HSS-E drills are comparable to HSS-G drills in terms of their essential properties, but the cobalt alloy gives them greater hardness and improved heat resistance. As a result, materials with very high strength, such as stainless steel, can also be machined. In our online shop, we offer you exclusively high-quality HSS drills in ground design, which are the ideal design for our plastic sheets. Especially the good chip evacuation and the self-centering drill tip are important features for soft materials, which include most plastics. The ground cutting edge, as well as the sharp drill head, cut excellently through the plastics and ensure very precise drilling and drill hole edges, which are only surpassed by our special drill made of solid carbide.
In principle, drills are extremely easy to clean. However, it makes sense to always clean the drills a little after use. Oiling the drills can also have a positive effect on their service life. Ideally, they should be stored in a small box so that the cutting edges always remain impeccable and sharp.
Especially with the hard drills made of solid carbide, it is very important to store them in the supplied transport case, because the drills are shock-sensitive and could be damaged during transport by colliding with other drills.
Drills are made of high quality steel alloys and can be recycled excellently by melting them down. So don't throw away old, dull drills carelessly and instead take them to the recycling yard, which will sort and recycle the drills according to carbide or high-speed steel. This is the only way to save valuable resources that are needed for the production of tools, drills and milling cutters made of solid carbide or HSS. If you have collected several drills, there are also many online suppliers who buy up the metal scrap at fair conditions.