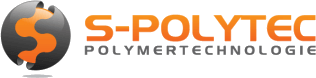
Aluminium composite panels are very rigid and stable. The composite structure consists of aluminium layers in 0.25 mm thickness on both sides with a polyethylene (PE) core. The total thickness of these panels is 3mm. The surfaces are lacquered and covered both sides with a protective film which can easily be peeled off.
Incl. 19% Tax
Incl. 19% Tax
Incl. 19% Tax
Incl. 19% Tax
Incl. 19% Tax
Incl. 19% Tax
Incl. 19% Tax
In our online shop, we offer you aluminium composite panels in a thickness of 3mm in various colours and designs in millimetre-precise cuts at rock-bottom prices. Depending on the colour, the surfaces of the panels are partly matt on both sides or matt on one side and glossy on the other. In addition, we also offer aluminium composite panels with a brushed structure or a fine metallic effect.
Buy your aluminium composite panels conveniently online in the formats you need and benefit from our attractive quantity discounts. Our cut-to-size configurator for our customised plastic sheets is very easy to use. Simply enter the required dimensions for length and width in millimetres (not centimetres). The price calculation takes place in real time and automatically calculates quantity discounts depending on the weight, so that you always get the best price for you.
Thanks to automated cutting optimisation, leftover cuttings that are not required are used for further orders where possible and you are not charged for them. You only pay for your cuts.
The cuts are made on special panel saws for horizontal cutting with variable speed adjustment and laser-assisted computer control. For this reason, we are able to guarantee the very low production tolerances of only +/-1mm for our blanks made of aluminium composite material.
Thanks to an optimised storage system, we are not only able to stock our aluminium composite panels in all colours and designs in very large quantities, but also to store any offcuts for further orders. The leftovers do not have to be disposed of, which has a positive effect on our favourable prices and on the environment. Due to the high storage capacities of the coloured aluminium composite panels, we can also achieve attractive purchasing conditions, which again has an effect on our pricing.
Our low-cost aluminium composite panels naturally comply with all standards such as REACH (EU Chemicals Regulation) or RoHS (Regulation on the Prohibition of Hazardous Substances in the Electrical and Electronic Industry) and are manufactured in accordance with DIN and ASTM standards, as well as ISO 9001:1500 (requirements for the certification of quality management systems) and ISO 14000:2004 (environmental management systems - requirements with instructions for use). This way you can be sure to get only the best quality at the best prices.
NOTE: Due to the pallet size for standard shipping, our blanks in the online shop are limited to 1500mmx1000mm. Larger formats are certainly possible, but only available on request due to different shipping costs. Our friendly team will be happy to inform you about delivery times and conditions.
Do you need company signs with contour milling, rounded corners, cut-outs, hole milling or similar from aluminium composite panels? Thanks to our modern panel saws, millimetre-precise cuts exactly to your specifications are no problem. With our CNC milling centres, we can also mill almost any conceivable shape for you in contour, so that (almost) no wishes remain unfulfilled.
Simply send us your enquiry with details regarding the colour of the aluminium composite panels, the required quantity and, in the case of milled parts, a design drawing or sketch with dimensions. Our competent staff will then contact you immediately and send you a customised offer.
We process the following formats: DXF, DWG, STEP or IGES. Furthermore, we are able to convert AI and EPS files.
The delivery of your cuttings from our aluminium composite panels usually takes place 3-4 working days after receipt of your order. The cuttings are normally made one working day after your order is received and are prepared for dispatch after quality control has been completed. Depending on the total weight of your order and the size of the cuttings, the goods are shipped as a parcel with a parcel service provider or with our partner forwarding agent on a pallet. As soon as we have registered the goods for dispatch, you will receive an e-mail from the relevant shipping service provider with a tracking number. Please note that shipping may take 1-2 days from the time of delivery.
Before your order is handed over to shipping, all your blanks are checked for compliance with the cutting tolerances. Only when all items of your order have passed the quality check will your order be carefully and securely packed and registered for shipment for collection. For the sake of our environment, we only use packaging material that can be fully recycled. For example, sturdy cardboard made from recycled paper.
NOTE: To protect the surfaces from damage, all our aluminium composite panels are provided with a protective film on both sides, which can be easily removed.
Aluminium composite panels are characterised by their enormous rigidity and comparatively low weight. Due to their UV and weather resistance, the panels can also be used excellently outdoors and withstand adverse weather conditions, frost and UV radiation for many years. The building sector in particular takes advantage of this and uses the stable panels as weatherproof cladding for facades and living spaces. The robust panels are also used as privacy screens or partitions on balconies and are an inexpensive alternative to HPL panels. In addition, roofers often use the sheets as a finish for flat roofs or as cladding for the underside of roof overhangs. Aluminium composite panels are also used in window construction. For example, as cladding for roller shutter boxes or as weatherboards for windows and doors.
However, aluminium composite panels are not only used outdoors. Especially in the kitchen, the panels with an attractive surface are used as an alternative to the conventional tiled backsplash, because aluminium composite panels are very easy to clean. In the bathroom, too, the waterproof panels are an attractive alternative to tiles. For example, as wall cladding in the shower cubicle.
Another very frequent use of aluminium composite panels is in advertising technology. From perimeter advertising for the local football club, to advertising signs and information boards for companies, to company lettering in contour milling. The light and stable sandwich panels are also often used in trade fair construction. It is not uncommon for the signs to be laminated with foils, inscribed using a plotter process or covered with a digital print in order to achieve an appealing and eye-catching advertisement. Many agencies and printers also offer their services in the private sector to print decorative wall designs with large-format images on aluminium composite panels. This is done either by printing directly on the panel or by printing on a self-adhesive digital printing film and is an attractive and unusual alternative to printed images on a canvas.
In vehicle construction, aluminium composite panels are used due to their low weight, for example, for the production of box bodies for trailers and trucks or for the interior panelling of delivery vans.
Aluminium composite panels are panels made of aluminium and plastic in a sandwich construction. They are manufactured in a special extrusion process. In this way, the aluminium face sheets are inseparably bonded to the plastic core, which is usually made of polyethylene (PE). Aluminium composite panels are often generally referred to by the brand name AluDibond®. The abbreviations ACP (aluminium composite panels) or ACM (aluminium composite materials) are also very common. The combination of aluminium and plastic creates a synergy between the individual material properties, which results in the enormous rigidity of the aluminium composite panels. Thanks to the polyethylene core, the panels are significantly lighter than solid aluminium panels of the same thickness. Another advantage of the sandwich construction is the easier machinability compared to panels made exclusively of aluminium.
Aluminium composite panels are available in a wide variety of designs. They are available in different thicknesses, whereby the thickness is mainly determined by the thickness of the plastic core. Depending on the quality of the panels, the aluminium face sheets have a thickness of 0.1-0.35 mm. The higher the thickness of the top layer, the better the quality of the composite panels. In addition, the inherent rigidity and stability of the panels increase with the thickness of the aluminium layers. This is an important aspect, not least for larger panel formats. The face layers of our aluminium composite panels are around 0.30mm.
In their original form, composite panels have a typical aluminium-coloured surface. However, aluminium composite panels are available in almost all colours and decors. From white and black to coloured panels according to the RAL colour system, to colours with a metallic effect or in wood decor, almost no wish remains unfulfilled. Structured surfaces, such as our composite panels in brushed aluminium with a high-quality stainless steel look, are also available with aluminium composite panels. To ensure that the colour remains permanently intact and does not fade due to constant weathering, the surfaces are stove enamelled in several layers and sealed with a clear varnish. This makes the coloured aluminium composite panels not only suitable for outdoor use, but also resistant to impacts or scratches.
NOTE: All the aluminium composite panels we offer are weatherproof and have a core made of solid polyethylene in black.
Our aluminium composite panels with a thickness of 3mm consist of two approx. 0.2mm-0.3mm thick aluminium cover layers (depending on the colour of the aluminium composite panels) and a black plastic core made of polyethylene. These sandwich panels with a physical density of approx. 1.3g/cm3, offer enormous rigidity and stability despite their comparatively low own weight.
Aluminium composite panels have a high bending and breaking strength and excellent resistance to chemicals. Furthermore, our aluminium composite panels are UV and weather resistant. This makes the weatherproof panel ideally suited for permanent outdoor use. With a temperature range of -40°C to +80°C, the panels are insensitive to frost and can also withstand high summer temperatures in strong sunlight.
The thermal expansion is just one tenth compared to normal plastic sheets. This makes these panels ideally suited for cladding large surfaces, for example, to enhance facades through the aesthetic appearance or the painting of the surfaces on both sides.
NOTE: Detailed information on the physical and thermal properties of our aluminium composite panels can be found in the detailed product description and the associated data sheets.
Cutting our aluminium composite panels is possible with simple tools. For example, cut-outs or radii can be made very easily with a jigsaw. For straight cuts, we recommend using a hand-held circular saw, as this is the best way to ensure the straightness of the saw cuts. Due to the aluminium cover layers on both sides, a fine-toothed saw blade for metal should be used. The speed, as well as the feed rate, should be selected in the medium range - similar to our plastic panels - in order to avoid melting the PE core of the sandwich panels.
CNC milling is another possibility to bring the aluminium composite panels to the desired size. In contrast to sawing, milling offers significantly more flexibility in terms of shaping and, in addition to cut-outs, also allows the aluminium cover layers to be engraved so that the black polyethylene core becomes visible.
Due to the low thickness, cuts can also be made by punching or water jet cutting. However, special equipment is required for this.
WARNING: Cutting with a CO2 laser is not easily possible and requires a special laser unit with sufficient power.
We recommend a metal drill for drilling aluminium composite panels. When drilling, the panels should rest on a flat surface to prevent the 3mm thick panels from bending due to the pressure. Due to the hard, smooth aluminium surface, the drill holes should be pre-scored with a marking tool or centre punch. This prevents the drill from slipping and ensures precise positioning of the drill holes.
TIP: With our CNC milling, we can cut your composite panels into any shape and also carry out precise hole drilling.
Aluminium composite panels can be installed indoors and outdoors in a variety of ways. As facade panels or wall cladding, for example, they can be mounted by gluing or directly screwing them to the substrate. In addition, mounting with spacer sleeves made of stainless steel or aluminium is common practice and is implemented especially for lettered advertising signs for a more appealing appearance. Riveting to a metal substructure with rivets in the matching colour, as well as joining the sandwich panels together, is another widely used method for mounting aluminium composite panels.
Our composite panels in sandwich construction are extremely resistant to bending, but can be bent to a certain extent due to the low thickness of 3mm. However, a bending device should be used for an exact bending radius. A bending bench is recommended for bending at a certain angle.
By milling grooves with a special milling head, the bend-resistant aluminium composite panels can also be bent at a perfect right angle. This is practised in particular for weatherboards on windows or flat roofs.
WARNING: If aluminium composite panels are bent or bevelled, this cannot be undone without having a negative effect on the appearance of the surface.
When bonding aluminium composite panels, it depends on the intended use. For large-area bonding as facade panels or wall cladding, a powerful assembly adhesive such as our MS polymers is most suitable. This adheres both to the aluminium top layer and to almost all substrates found in the building sector, such as tiles, concrete, sand-lime brick, wood or plasterboard. An MS polymer is also very suitable for bonding the composite panels together, or for sealing butt edges and corners when the panels are used, for example, as wall cladding in shower cubicles or damp rooms. Solvent-based adhesives are not recommended because the solvent has no effect on aluminium and cannot dissolve the metal surface. Instead, the solvent can attack the paintwork. With our two-component adhesive Plexus MA300, bonding of metals to each other or to plastics is possible, so we recommend this adhesive for smaller bonding jobs, or for making enclosures by gluing. Our plastic adhesives Ruderer L530 or Technicoll 8008 are also very suitable for bonding the aluminium composite panels to a wide range of materials.
Printing on the aluminium surfaces is possible without further ado. Various printing processes are available for this, such as screen printing or the direct printing process in digital printing. With direct printing in particular, digital photos can be printed on the surfaces with little effort to achieve high-quality wall pictures as decoration with an appealing look. However, this requires special plate printers, such as those used in large print shops or by advertising agencies. Our white aluminium composite panels are most suitable for printing, as the neutral surface does not distort the colour effect. For a special effect, brushed aluminium surfaces with a stainless steel look are also used quite often. Especially with black and white pictures, you get a very special look with a high-quality surface feel. It is not uncommon to use transparent acrylic glass plates to protect the printed surface or to improve the depth effect of the prints.
As an alternative to printing directly on the panel surface, digital prints can be printed on a self-adhesive film. This is then glued to the aluminium top layer. Depending on the intended use, a protective laminate is applied on top to prevent the inks from fading due to ultraviolet radiation. This process is used especially for large-format advertising signs, because it not only offers maximum flexibility, but is also usually much cheaper than a comparable direct print.
The panels in sandwich construction are extremely durable and therefore do not need to be replaced or renewed at regular intervals. The panels do not decompose and are corrosion-resistant. This means that aluminium composite panels can be classified as very environmentally friendly. If the use of the weatherproof panels is no longer desired, the panels can be disposed of at the recycling centre and thus professionally recycled.
Dibond® and Butlerfinish® are registered brand names of 3A Composites Holding AG.