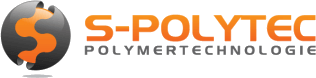
Perforated plates made of plastic are needed for many applications. We explain what perforated plates are and how they are manufactured.
Perforated plates are needed in a wide variety of applications, for example for washstands, special screens, or for filter systems and sorting plants.
As different as the areas of application for perforated plates can be, the requirements for the perforated plates themselves are just as individual, in terms of the material or geometry of the perforated plates.
You will not find what you need for such individual requirements in the DIY store, so the motto is to either make the perforated panels yourself or have them made.
Perforated plates are, as the name suggests, plates made of plastic, metal or other materials whose surface allows the passage of air, liquids or solids in certain sizes through recesses in the form of holes. The holes do not necessarily have to be round and perforated plates with elongated holes are not uncommon.
A very simple example of perforated panels are computer housings, which usually have a large number of small holes (or slots) on the side or back to allow sufficient air circulation for cooling processors, graphics cards and all other components. The same applies to monitors, TV sets, stereo systems and almost all electrical devices that are expected to generate heat.
However, perforated plates are not only used for the discharge of warm air, but also play a very decisive role in filter and sorting technology, among other things. Perforated plates can be used, for example, to separate liquids from solids, as is the case in sewage treatment plants or in filter systems in swimming pool technology. But perforated plates are also used to sort solids according to different sizes. An example of this is sand and gravel plants, which use the hole size of the perforated plates both to separate the fineness of the sand and to sort the conveyed gravel according to the size of the pebbles. The same applies to conveying and sorting systems in mining and open-cast mining.
As already mentioned in the introduction, the size and geometry of the perforated plates can vary greatly depending on the intended use. From small dimensions of the perforated plates to large-sized perforated plates. Perforated plates with very many small holes, or long holes, slots or large recesses. The search for standard solutions is almost impossible, so the solution for the production of perforated plates is almost always custom-made.
In order to create individual perforated panels according to the requirements of the intended use, there are different solutions.
The most common production techniques are probably manual production, production using CNC technology or punching perforated plates. However, each of these techniques has its advantages and disadvantages, which we would like to explain to you in more detail below.
Manual production is more suitable for small quantities and prototypes, because the production of perforated plates by drilling or sawing the holes involves a relatively high effort.
The data of the design drawing must be transferred to the later perforated plate by very precise measuring. This is done by marking or scribing with a scribing needle. To prevent the drill from slipping when drilling holes, punching, i.e. hammering a round notch into the plate with a metal pin (centre punch), is quite helpful, but this is no guarantee that the position of the hole will be exact. Recesses or oblong holes require a high degree of concentration when sawing and again a lot of time. Reworking with an arrow or sandpaper increases the accuracy but also the time needed to make the perforated plates.
The manufacturing tolerances of the manufactured perforated plates also tend to be in the lower range, since when holes are drilled manually, it cannot be guaranteed that they are made exactly in the position required by the sketch or design drawing. The higher the run of the perforated plates to be manufactured, the greater the probability that the accuracy of the manufacturing tolerances will decrease during the manual production of perforated plates.
The manufacture of perforated plates by CNC production is very flexible and is equally suitable for the production of small quantities, prototypes or perforated plates in series production in high runs. Many different geometries and not just simple holes can be produced without significant effort. Long holes, crosses, recesses, chamfers or countersinks are also easily possible by milling with a CNC milling machine such as the one we use in our production.
The manufacturing tolerances of perforated plates by CNC production are extremely low, even for series production. Our modern CNC milling centres, for example, work with a very low tolerance of just +/- 0.3mm on the X and Y axes.
To produce perforated plates by milling with a CNC milling machine, it is necessary to generate a milling programme. This means that a design drawing must be converted into a format that can be processed by the milling machine so that the milling machine can make the cut-outs and drill the holes exactly according to these contours. However, this step is only necessary once and, depending on the complexity of the perforated plates, only requires a very small amount of time compared to manual production. The milling of the perforated plates themselves again requires time that depends on the size of the perforated plates. The number of holes, recesses or slots to be milled, as well as the thickness of the perforated plates, also play a role in the time required.
In contrast to the production of perforated plates by punching, CNC production of perforated plates is not so limited in the thickness of the plates. The maximum plate thickness is only limited by the maximum feasible milling depth of the Z-axis, which, depending on the size of the CNC milling machine, also allows for very thick perforated plates.
With our milling machines we have the possibility to produce perforated plates up to a size of 4000mm by 2000mm in length and width, as well as a maximum thickness of 200mm. In exceptional cases, thicknesses of up to 240mm are also possible, but this also requires a corresponding effort for the set-up of the milling plant.
Another advantage of manufacturing perforated plates by CNC milling is the flexibility in making changes to the geometry of the perforated plates. Even changes to the hole sizes, the number of holes or the addition of recesses require comparatively little time and cost, because in such cases only adjustments to the respective milling programme are necessary.
The punching of perforated plates is usually only used for very high quantities and rather thinner materials, so that the production of the perforated plates remains profitable. Depending on the geometry and complexity of the perforated plates, the production of the punching blades can cost up to several tens of thousands of euros, and these costs must be covered by a correspondingly high run in the series production of perforated plates.
The advantage of punching perforated plates lies in the processing speed of the plastic plates to be punched, because the punching process is comparatively quick, so that high quantities can be produced within a very short time.
However, punching perforated plates also offers little flexibility in the production of perforated plates, because if changes have to be made to the perforated plates, it is also necessary to adapt the punching knives, or even to manufacture new punching knives, which can sometimes be very cost-intensive. Furthermore, punching with high material thicknesses, especially with harder plastics, is not unproblematic and can lead to quite high wear of the punching knives, which is again associated with high costs. For this reason, punching of perforated plates is usually only used up to a plate thickness of 10mm. With harder plastics, the maximum plate thickness can even be less.
Thanks to modern CNC milling centres according to the latest standards, it is easy for us to manufacture your individual perforated plates. You can choose from a variety of different plastics that we carry in our online shop. This ensures that the right plastic for the production of perforated sheets is also guaranteed to be available for your intended use.
With our milling service, it is possible for us to produce perforated plates up to a size of 4.0x2.0 metres. Even perforated panels with high thicknesses of up to 200mm are possible for us without further ado. If required, the perforated panels can also be provided with chamfers on the edges, countersinks for screw connections or recesses. With a very low manufacturing tolerance of +/-0.3mm, we ensure the highest accuracy of the manufactured perforated plates exactly according to your design drawing, regardless of whether the perforated plate is a prototype or a series production in high quantities.
For the production of the milling programmes for your perforated plates, we only need a design drawing. We can easily process files in DXF format or DWG format. We can also create milling programmes from three-dimensional STEP or IGES files. Furthermore, we are able to convert EPS files or Adobe Illustrator files in such a way that the production of your perforated plates is possible on our CNC milling machines.
Detailed information about our milling service can be found on the information page about our milling service.