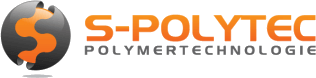
A lot has happened again. Follow the progress of the renovation work on the new location and learn about the importance of sustainability and carbon footprint.
The renovation work is progressing quickly and the first shelves are already in place. So things could start very soon, but before that happens, a few things have to happen. We reveal what is meant by this in this blog post.
We have already reported several times about the new location in the Hammereisen industrial estate. A few weeks have now passed since the last blog post and a lot has happened with the renovation. The painting work in the main hall has been completed and even some of the adjoining rooms have already been renovated. In this blog post, however, we do not just want to write about what we have already done, but also what the next steps will be. Which machines will be used here and when can we start production? We will try to answer these questions in detail in this post.
The shelves are up and it can be put away
The warehouse for silicones, adhesives and assembly materials is ready. A few shelves are still missing, but they will be installed in the near future. The magazine gives us almost 70% more space for drills, screws and rivets than we had at the previous location and so we will gradually add a whole range of other products for processing and assembling our plastic sheets to the range. A few new products are even here already, just waiting to be sorted onto the shelves.
First of all, there are the alkoxy silicones of our own brand S-Polybond SILIKONprofi, which we have been selling in our online shop for a few days. This is a particularly environmentally friendly silicone, which is characterised by a whole range of positive properties. However, we are not talking about silicones here, so we do not want to go into this topic any further and will deal with it in a separate blog article. Fittingly, the round cords have also arrived with us. At the moment, the 23 Euro pallets are still in the production hall, but that will change in a few days. The countless boxes with various façade screws and balcony screws that are temporarily stored in the hall will also find their final storage place soon, and then we could almost start shipping from this location.
New packing stations have been purchased so that we can get started immediately once all the official matters have been settled. New electric high-lift trucks for the high-bay warehouse have also arrived. Unfortunately, the paperwork is still giving us a bit of a hard time at the moment. Although all the documents are very well prepared and all aspects relating to fire protection and occupational safety are also guaranteed, our authorities need a little time for the application for the change of land use. A little more than we would like, because the application has been in progress for several months now. The only thing that helps here is to wait, drink coffee and use the time effectively to perfect the site.
We have already mentioned several times that the new location is significantly larger. This means that we not only have more space for shelving, which offers significantly more berths to expand our range of plastic sheets, but also sufficient space for more machines. We will move a panel saw from the current location in Goch to Kranenburg. The four CNC portal milling machines will also move to Kranenburg. The remaining saws, as well as the three CO2 laser systems, however, will remain in Goch.
With one saw, however, we won't get far in Kranenburg, so we have already ordered another one. This is a highly modern saw-storage combination in which the saw pre-sorts all the boards overnight in the right order for processing the next day. For this purpose, the saw has 16 storage bays, each with an area of 4.0 by 2.5 metres, which can be loaded up to 2 metres high. This would allow us to store over 10,000 aluminium composite panels in 3mm thickness. Even if we store HPL sheets with a thickness of 8 mm, we would have a capacity for 4,000 HPL sheets with the saw-storage combination. The advantage of this saw, however, is the integrated storage management, so that we can store both aluminium composite panels in various colours and HPL panels in various thicknesses and decors in this warehouse. The saw stores the panels fully automatically and, based on the cut sizes ordered in the online shop, can always fall back on suitable formats or remnants without our employees having to intervene here. This saves an enormous amount of time and racks for off-cuts, which have a minimum size, are also no longer needed. However, this fully automated saw-storage combination also requires a lot of space. The footprint for this saw is 20m in width and at least 18m in depth.
In addition, the purchase of a special saw is planned for the near future, with which it will be possible for us to offer solid and hollow plastic rods cut to the millimetre. This will require some adjustments to the online shop, but thanks to our in-house programmers, this should be the least of our problems. This saw could then possibly also be used for cutting our optical profiles made of aluminium or our substructure profiles for façade cladding. When that will be, however, cannot be answered concretely at this point.
Compliance with climate targets is also an important issue for us, and so we have decided to make the new location as climate-neutral as possible. This includes, among other things, the energy demand, which is not exactly low due to our panel saws and CNC milling machines. In order to achieve environmentally friendly power generation, the hall roof is to be equipped with a very large photovoltaic system. With a usable area of approx. 1500 square metres, 150-190 kilowatt peak could be generated, depending on the efficiency of the modules. Converted, this amounts to about 140,000 KW/h - 240,000 KW/h per year and thus covers the company's own needs three to four times over.
Although the heating system is quite modern, it is still heated with natural gas. This heating system ensures that the offices are all kept at a comfortable temperature so that our fingers do not freeze on the keyboard when we write these blog articles. The hall is also heated with gas via this system. Here, 12 large radiant panels ensure a constant temperature in the halls when it gets icy outside. However, gas has not only become very expensive, it is also not exactly sustainable, because natural gas has to be extracted at great expense. For this reason, we decided on a heat pump system, which does need electricity to heat the water, but thanks to the photovoltaic system we generate this ourselves, so we can heat completely self-sufficiently. The best thing about the future system, however, is that it can be used to cool the offices in summer, eliminating the need for energy-guzzling air-conditioning units.
Maybe only a small aspect, but still worth mentioning, we have already changed all ceiling and wall lights in the offices to energy-efficient LED daylight fixtures. The old fluorescent tubes in the hall and the high-bay warehouse have also been replaced with LED tubes. This saves us around 60% energy just for lighting. In order to increase the efficiency of the lighting, everything in the production area was repainted in bright white.
Like us on Facebook or Instagram to never miss any news again.
We hope you enjoyed the post and are glad you took the time to read it. Feel free to call or email us with any suggestions or questions.