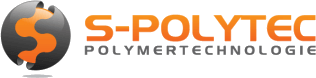
Big hall, big plans, big commitment. Follow the elaborate process of renovating our enormous production and storage space and find out what we have in store to offer you even more in the future.
Renovation work on our new large-scale production and storage facility on the Hammereisen industrial estate in Kranenburg is in full swing. The progress is now clearly visible and the move-in of our state-of-the-art machines, the stored products and the remaining departments is getting closer and closer. You can find out what we have achieved so far and what is still planned in this blog post.
The renovation of our huge production and storage area at our new location in the Hammereisen industrial estate in Kranenburg is in full swing, because well renovated is half done. In a few weeks, the arrival of our production is planned. For this, all machines, such as CNC portal milling machines, CNC panel saws and ultra-modern CO² laser cutters must be loaded onto large lorries professionally and with the utmost care and transported with them to Kranenburg. All stored plastic sheets and small materials such as screws, rivets and adhesives must also be packed at the old location and transported to the new company premises.
To ensure that production can continue smoothly parallel to the move, we prepare the new premises perfectly. This is to ensure a smooth process when the machines and products arrive. After all, they have to be stored, placed and put into operation as quickly as possible after transport. In addition to cleaning and repairing the hall, the magazine and the adjoining rooms, the preparations also include fulfilling basic guidelines, such as the strict requirements for fire protection. In addition, there is a large open area at the rear of the site that offers possibilities for expanded storage capacity. However, as the paved area is currently more reminiscent of a turbulent off-road race track, we still have a lot to do there as well. So it remains busy and exciting...
As our production hall is still empty at the moment, it offers the perfect opportunity to bring everything up to a high shine.
Our new company premises were previously operated by a tool hardening shop. Over the years, an inch-thick layer of metal dust had built up on all surfaces and walls. We spared no effort and set about polishing everything to a high shine so that our production has a fresh new start and no unwanted dirt particles can be deposited on our high-quality plastic sheets and machines. In this way, we can ensure the optimum quality of our products and services in the future.
The major project began with the dismantling of unneeded installations and control panels. In addition, the huge, heavy partition walls were removed from the enormous hall to create an even more spacious production and storage area. For the most effective approach, it was then decided that we would work our way down from the top. So, without further ado, an elevating work platform was purchased, because the ceiling height is about 12 metres. This brings us to the issue of fear of heights, because many of the planned works are at dizzying heights.
First, the several hundred metres of light strips were freed from the thick layer of dust with a hoover and then washed off by hand. In the course of this, the old fluorescent tubes were replaced with energy-saving LED tubes. This involved about 300 tubes, just to give a small impression of the dimensions. Since the climate balance is very important to us, we are particularly pleased that we were able to positively influence it in this way. Once this was done, the steel girders and the heavy-duty crane with a lifting capacity of 16 tonnes were cleaned. The crane can be used over the entire length and width of the hall. This makes it much easier to transport the plastic sheets, some of which are quite bulky and heavy depending on the material. The layer of dust deposited on it was so massive that the colour of the girders and the crane was determined by the colour of the dirt. And so matt black suddenly became bright yellow.
Highly motivated by the clearly visible changes, we then set about beautifying the walls. These were also vacuumed by hand, centimetre by centimetre. This work took several days, but already after this step a significant difference was visible. After all the dust had been removed, the painting could begin. The entire walls were painted in bright white, giving the huge hall a new shine and a bright, clean and appealing atmosphere.
The enormous hall will be used in future for the production area and storage of our high-quality plastic sheets. In addition to the installation and commissioning of the old and new machines, the storage systems for storing our sheets, some of which are just under 5.5 square metres in size, will have to be assembled. Due to the enormous space gained, we will soon be able to offer an expanded product range and also store more, which will allow us to shorten delivery times even more. The focus is primarily on an expanded selection of our decor panels made of high-pressure laminate. The extremely versatile HPL panels can be used equally well indoors and outdoors and, depending on the version, are approved for balcony cladding in accordance with the ETB directive. We will soon be offering the scratch-resistant and bending-resistant plastic panels in further designs, colours and surface decors.
From the large main hall, there is direct access to the separate high-bay warehouse for assembly materials such as head-painted screws and rivets, drills, as well as for hot-air equipment, adhesives and silicones. At the moment we are busy in this area to meet the requirements of the fire protection regulations to prevent the spread of fire and smoke. Unfortunately, the ceiling there is covered with wooden panels, which have to be completely removed and replaced with fireproof cladding. Furthermore, there was a false ceiling there until a few days ago, which we also removed. This provides enough space to install the high shelves that reach up to the ceiling. Here, too, we are planning to expand our product range thanks to the additional storage capacity. We are particularly pleased that it will soon finally be possible to offer the alkoxy silicones of our own brand S-Polybond SILIKONprofi. The high-quality alkoxy-based adhesive and sealant is absolutely MEKO-free and meets all the requirements of professional users in commercial areas as well as those of not-so-experienced hobby home craftsmen without exception.
To enable a constantly growing product range with the fastest possible delivery times, you can never have enough storage space. Therefore, we are planning to build another warehouse on the vacant area behind the building which will be used as buffer storage for plastic sheets, pallets and packaging material. This is currently in a rather bad condition, because in some places almost half a metre high elevations have formed in the paved area. Therefore, all paving stones have to be removed before the subsoil can be smoothed with the help of small excavators and prepared for the new paving.
With its enormous size, the new location offers numerous options for implementing new plans and bringing all departments together. The renovation and installation of the state-of-the-art media room, which is being prepared for meetings and visitor reception, is slowly taking shape. The cables for the connections of the large monitor for presentations have been laid as far as possible and painting has begun. In the near future, the large meeting table will arrive and provide space for sixteen people. In this room, new plans are made, new products are planned and philosophised.
We are constantly working to optimise our range, product presentation and all processes in order to guarantee perfect service and products of the highest quality. There are many adjoining rooms that allow us to expand and develop certain areas of the business. As all departments will soon be reunited in one place, improved communication will be guaranteed. Ideas and information from the different departments can be exchanged and implemented in the shortest possible time. Of course, this already worked well before, but it will lead to even faster results in the future. Among other things, in the product development of further extremely high-quality products of our own brand S-Polybond. Through this, we sell the most advanced adhesives and sealants, as well as matching accessories.
For the filling of the high-quality adhesives of our own brand S-Polybond, a separate room is equipped with a filling line. Our adhesives have been specially developed for bonding different plastics. The technical plastic polyethylene is normally very difficult to bond, so we have developed a special 2-component adhesive. The special adhesive PE-adhesive PEprofi achieves perfect strengths and ensures a permanent and secure connection of the joined parts. In addition, we also offer these adhesives especially for use on polypropylene (PP), acrylic glass (PMMA) and ABS.
In addition, a workshop is being built for our IT administrator/company technician, or rather 'the girl for everything'. He will have his domain there to drive forward the technical development with regard to the automation and process optimisation of the company and to carry out quality checks of the blanks. The smallest deviations are detected, whereupon the saws or milling machines are readjusted. This ensures precise and clean cutting at all times. In addition, he carries out the regular maintenance of the production machines and repairs affected components if necessary. Thanks to immediate repairs directly on site, production is never interrupted in the long term.
We still have a little work to do... We can't wait to finally be under one roof with all departments and staff and to be at our best together.
We hope that you have enjoyed this article and that it has stimulated curiosity about future changes and news. Of course, we will keep you updated on upcoming progress. To make sure you don't miss anything, feel free to follow us on Facebook and Instagram.
Your Melina from S-Polytec