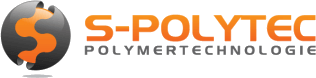
We explain what plastic is and everything you need to know about plastic and its processing.
Plastics are substances that are synthesised from the individual building blocks, the monomers, and contain further additives. In a chain reaction called polymerisation, the monomers are bonded to each other and thus form a chain, the macromolecule. The monomers themselves are usually liquid or gaseous. Through the linkage, the molecules gain mass and take on a solid form. Depending on whether the monomers simply string together or a monomer combines with several molecules, either a chain or a network is formed. When a chain is formed, it is called a thermoplastic; when a network is formed, it is called a duromer or elastomer. A close-meshed network results in the duromers (outdated thermosets), plastics that can no longer be deformed by reheating. A wide-meshed network produces the elastomers or also called rubber. The monomers used determine the polymer name, depending on which monomers are polymerised into a polymer, e.g. polymerising styrene results in polystyrene, polymerising methyl acrylate results in polymethyl acrylate. This is how the polymers are first produced. Additives such as colour pigments, antistatic agents, fluids or fillers are then added to produce the finished plastic. Most plastics are traded in granular form and can thus be easily processed by plastics processing machines such as extrusion lines or injection moulding machines by thermal action to produce finished parts or semi-finished products.
Depending on the monomer used, there are a variety of different plastics such as ABS, Polytsyrol, PVC, PE, PP, PEEK, PMMA, PC, PVDF, PTFE, PA and many more. All these plastics have different properties and each has its advantages and disadvantages. Below, the most important and the most common plastics are explained and the main properties are described.
The first plastic to be developed in the styrene family was polystyrene. Styrene is very easy to polymerise radically into polystyrene. The resulting plastic is amorphous, ( transparent ) has very high transparency and is very brittle. Due to its high brittleness, this plastic cannot be used in many applications. Attempts have been made to make PS more impact resistant in order to increase the range of applications. By incorporating small rubber gels into the matrix, SB (styrene butadiene) was born.
Because polystyrene is very non polar due to its molecule and can therefore be tempered very quickly by non polar solvents, it had to be chemically stabilised against non polar solvents such as petrol, diesel or oil. This was achieved by adding acrylonitrile. The impact-resistant component was also retained in the material, resulting in ABS (acrylonitrile-butadiene-styrene).
Semi-finished plastic products are products made of plastic that are further processed, such as plastic sheets, pipes or profiles. The further processing of plastic semi-finished products requires plastics expertise. The processing parameters for the individual plastics differ, sometimes very significantly.
The bonding of plastics is a field of expertise in itself. In general, it can be said that amorphous plastics can be bonded well and semi-crystalline plastics are much more difficult to bond. To achieve good adhesion, the plastics should contain more atoms than carbon or hydrogen in the molecular chain. These create polarity in the molecule and can thus be chemically attacked.
The most popular method of bonding plastics is so-called cold welding. This involves the use of a solvent that penetrates the material and dissolves it. If two such gelled surfaces are joined together, the molecules will bond with each other. After the diffusion of the solvent, the molecules remain bonded to each other, forming a very strong bond.
This bonding process is known as the 'gel bonding' process.
When using this bonding method, always pay attention to the stress balance of the plastic parts. If the parts contain very high internal stresses due to processing, these can be selectively stressed by the action of solvents, so that the parts can warp, sometimes severely, after drying out.
If different plastic parts are used, they must be bonded together very firmly.
If you want to bond different plastics or plastics with other materials, you cannot avoid bonding them chemically. There are two major differences between 1K and 2K adhesives. <1K adhesives are usually not aggressive reaction systems and usually cure by adding humidity or oxygen. Bonding large surfaces with these adhesives is not advisable, as the required curing component does not reach the adhesive.
The 2-component systems such as methyl methacrylate, epoxies or polyurethanes are much more reactive. MMAs in particular are highly recommended for plastic or plastic-metal bonding. A example product (Plexus MA300) can be found here. In this process, the molecules are chemically attacked and bonded. The resulting bond has enormous strength and can transfer forces very well.