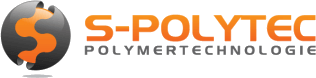
Valuable practical tips on the subject of plastic welding. Learn how to create the first welds in ABS, PE, PP or PVC for a secure and durable connection of your plastic parts.
Welding of plastic is a common joining method and is used very often, especially when bonding plastics does not guarantee a sufficient or permanent connection.
This is especially true for plastics that are difficult to bond, such as polyethylene or polypropylene.
To weld plastics successfully, however, there are a few points to bear in mind, which we would like to explain to you briefly and compactly below, so that you too can dare to make your first weld.
The welding of plastics is a very common method and differs significantly from classic metal welding. However, both welding methods have one thing in common. A perfect weld seam requires not only the appropriate expertise, but also a certain amount of practice, because as the saying goes, no master has ever fallen from the sky.
As is usual with tools, there are also different welding machines in different price ranges for plastic welding.
A hot air fan welder is most suitable for welding plastics because it is quite inexpensive compared to a handheld extrusion welder, which is very commonly used by welding shops.
A handheld extrusion welder, also known as a hand extruder, increases the welding speed many times over, making it cost-effective for shops that weld plastic together every day. However, such a hand extruder in a corresponding quality also costs at least 5,000 euros, so that the purchase is only worthwhile if several hundred metres of weld seams have to be welded every day.
The hot-air fan welder can be purchased at a much lower price, starting at around 300 euros, so that even the occasional welding of plastics is worthwhile. With this fan welder, quite good results can also already be achieved.
For very simple repairs, a simple soldering iron is often sufficient. However, this is not recommended for proper welding seams.
The welding rod must be suitable for the plastic to be welded
When choosing the right welding rod, it is very important that it is made of the same plastic as the plastic parts to be welded themselves. For this reason, there is also a suitable welding rod for all plastics that can be welded.
The strength of the welding rod is determined by the thickness of the plastic.
The thickness of the welding rod depends on the weld to be applied. If you want to weld two plastic sheets with a thickness of 2mm each, a 3mm welding rod will be quite sufficient. For thicker sheets, a thicker welding rod with a thickness of 4 mm-5 mm is recommended.
Matching welding rods in our online shop as yard goods at favourable graduated prices
It is important that only plastics of the same type can be welded together. So it is perfectly possible to weld polyethylene to polyethylene, or polypropylene to polypropylene. The same applies to welding ABS with ABS and all other plastics for which welding is a possible joining method instead of bonding.
Welding different plastics together is not possible and so polyethylene cannot be welded to polypropylene or polystyrene. The reason lies in the different chemical compositions, which do not allow a permanent bond to be made between them by welding.
The plastic surface contains an oxide layer that can have a significant adverse effect on the weld quality. Therefore, the surface of the parts to be welded, but also of the welding wire, should be removed with a deburrer or with a cutter knife. You will be able to see exactly how this is done in the video below.
We have taken the liberty of picking out a helpful instructional video for you on the subject of plastic welding, which was created by the Ostfalia University of Applied Sciences.
When welding plastics, make sure that both the welding rod and the plastic surfaces to be welded themselves heat up sufficiently so that the surfaces reach a level of fusion that is highly important for a durable and secure weld. If several weld seams are made on top of each other, for example because thick sheets are to be seamlessly welded together, it is recommended that the weld seams cool down completely before a new weld seam is made on top of them. Protruding or overflowing welds can be cut off later with a cutter knife or ground off with a sanding block to achieve a flat, flush weld.
ABS (acrylonitrile-butadiene-styrene)
Welding ABS is possible without any problems. The air temperature should be in the range of +270°C and +310°C to weld ABS plastics.
PS (polystyrene)
Polystyrene can also be welded very well. The air temperature for welding polystyrene should be between +270°C and +310°C.
PE (polyethylene)
Polyethylene cannot be bonded with conventional adhesives, so welding PE is common practice. However, PE can be welded well and very easily. The air temperature for a weld in PE welding should be between +220°C and +280°C.
PP (polypropylene)
As with polyethylene, bonding polypropylene is not straightforward. However, this does not apply to the welding of polypropylene and leads to good results. However, when welding PP, close attention should be paid to the temperature level and the heating time. Polypropylene burns quite quickly and the burnt material deteriorates the weld. The air temperature for PP welding should be between +230° and +280°C.
PVC (polyvinyl chloride)
When welding PVC, close attention must also be paid to the temperature level and the heating time. PVC also burns very quickly, forming hydrochloric acid which has a strong pungent effect when inhaled. The burnt PVC surface deteriorates the quality of the weld seam and the appearance, as burnt PVC immediately turns dark brown to black. The air temperature for PVC welding should be between +250° and +280°C.
We hope you enjoyed our article and that it was of some help to you when welding your plastic parts.